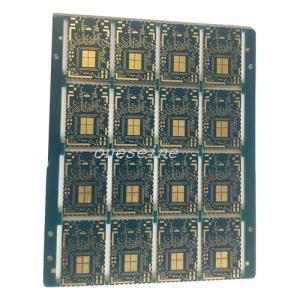
Add to Cart
8 camada Multilayer HDI PCB Custo Com Vias Cegos placas de circuito impresso Protótipo
Informações gerais:
Camada:8
Material: FR4
Espessura: 2,0 mm
Revestimento de superfície: ENIG
Especial: buraco cego, L1-L2, L3-L4, L5-L6, vias preenchidas e cobertas
Tamanho da placa: 2*6 cm
Máscara de solda:Não
Tela de seda: Branco
Nome: Placas de circuito impresso de 8 camadas
Prazo de entrega: 10 dias para amostras e lotes pequenos e médios
Sobre a cotação: Para o especial de vias cegas PCB, então a cotação precisa tem que fornecer o arquivo gerber ((DXP etc.)
Embalagem: embalagem interna: embalagem a vácuo/saco plástico embalagem exterior: embalagem de cartão padrão
Viais cegos:
As vias cegas são utilizadas para ligar uma camada externa com pelo menos uma camada interna.
Os furos de cada nível de ligação devem ser definidos como uma fileira separada.
A relação entre a profundidade do buraco e o diâmetro da perfuração (ratio de aspecto) deve ser ≤ 1.
O buraco mais pequeno determina a profundidade e, portanto, a distância máxima entre o
A camada externa e as camadas internas correspondentes.
Para mais detalhes, ver PCB de vias cegas e enterradas
Palavras-chave: Microvia, Via-in-Pad
HDI PCB de vias cegas:
As placas HDI, uma das tecnologias de mais rápido crescimento nos PCBs, as placas HDI contêm vias cegas e/ou enterradas e muitas vezes contêm microvias de 0,006 ou menos de diâmetro.Eles têm uma maior densidade de circuitos do que placas de circuito tradicionais.
Existem 6 tipos diferentes de placas HDI, através de vias de superfície para superfície, com vias enterradas e através de vias, duas ou mais camadas HDI com vias,Substrato passivo sem ligação elétrica, construções sem núcleo utilizando pares de camadas e construções alternativas de construções sem núcleo usando pares de camadas.
Tecnologias especiais utilizadas em placas de circuitos impressos HDI de qualquer camada:
Revestimento de bordas para blindagem e ligação à terra
Largura e espaçamento mínimos das vias na produção em massa, em torno de 40 μm
Micróvias empilhadas (de cobre revestido ou preenchidas com pasta condutora)
Cavidades, buracos de contra-enchimento ou fresagem em profundidade
Resistência à solda em preto, azul, verde, etc.
Material com baixo teor de halogénio na gama padrão e alta de Tg
Material de baixo nível de DK para dispositivos móveis
Todas as superfícies da indústria de placas de circuito impresso reconhecidas disponíveis
Como posso garantir vias de costura ou vias de moagem adequadas no meu projeto de PCB HDI?
1Determine Via Spacing and Distribution: Determine o espaçamento e a distribuição das vias de costura ou vias de moagem com base nos requisitos específicos do seu projeto.O espaçamento entre vias depende da frequência dos sinais e do nível desejado de isolamentoO espaçamento mais próximo proporciona um melhor isolamento, mas aumenta a complexidade e o custo de fabricação.
2Colocar vias ao longo das pistas de sinal: para assegurar uma ligação eficaz entre as camadas de sinal e o plano de solo, colocar vias de costura ou vias de solo regularmente ao longo das pistas de sinal.As vias devem ser distribuídas uniformemente e seguir um padrão consistenteConsidere a colocação de vias em intervalos regulares, como a cada poucos centímetros, ou em pontos críticos onde ocorrem transições de sinal.
3"Conectar vias ao plano de solo sólido: vias de costura ou vias de solo devem ser conectadas a um plano de solo sólido para proporcionar um caminho de retorno eficaz para os sinais.Garantir que as vias se conectam diretamente ao plano do solo sem interrupções ou lacunas.
4,Utilize uma relação de diâmetro e aspecto via suficiente: selecione uma relação de diâmetro e aspecto via adequada para garantir uma condutividade e dissipação térmicas suficientes.Maior através de diâmetros fornecem menor impedância e melhor condutividadeConsidere as capacidades de fabrico do seu fabricante de PCB ao determinar o tamanho da via, uma vez que vias menores podem exigir técnicas de fabricação mais avançadas.
5,Evitar comprimentos de via: Minimize o comprimento de via, que são as partes da via que se estendem além da camada de sinal.Via stubs pode criar discontinuidades de impedância e aumentar as reflexões de sinalUtilize vias cegas ou enterradas sempre que possível para minimizar os comprimentos dos tubos.
6Considere Arrays Via Ground: Em vez de vias individuais, você pode usar o solo através de matrizes ou através de cercas.Estes consistem em vias múltiplas dispostas em uma grade ou um padrão específico para melhorar o acoplamento entre as camadas de sinal e o plano de terraA terra através de matrizes fornece melhor isolamento e reduz a indutividade do caminho de retorno.
7"Realizar análise da integridade do sinal: realizar análise da integridade do sinal, incluindo simulação e modelagem, para avaliar a eficácia das vias de costura ou vias de aterramento.As simulações podem ajudar a identificar problemas potenciais, tais como variações de impedânciaAjuste a distribuição ou geometria da via conforme necessário com base nos resultados da análise.
Como posso determinar a impedância característica das linhas de transmissão no meu projeto de PCB HDI?
1Fórmulas empíricas: As fórmulas empíricas fornecem cálculos aproximados da impedância característica com base em suposições simplificadas.A fórmula mais utilizada é a fórmula da linha de transmissão de microstripA fórmula é: Zc = (87 / √εr) * log ((5,98h / W + 1,74b / W) Onde:
Zc = Impedância característica
εr = Permitividade relativa (constante dielétrica) do material do PCB
h = Altura do material dielétrico (espessura da traça)
W = Largura da pista
b = Separation between the trace and the reference plane (ground plane) It is important to note that empirical formulas provide approximate results and may not account for all the complexities of the PCB structure.
2Simulações do Solvedor de Campo: Para obter resultados mais precisos, simulações do solvedor de campo eletromagnético podem ser realizadas usando ferramentas de software especializadas.,a geometria de traços, materiais dielétricos e outros fatores para calcular com precisão a impedância característica.perdas dielétricas, e outros fatores que influenciam a impedância. ferramentas de software de resolvedor de campo, tais como Ansys HFSS, CST Studio Suite, ou Sonnet, permitem que você insira a estrutura do PCB, propriedades do material,e traçar dimensões para simular a linha de transmissão e obter a impedância característicaEstas simulações proporcionam resultados mais precisos e são recomendadas para aplicações de alta frequência ou quando o controlo preciso da impedância é crucial.
Quais são alguns desafios na implementação da tecnologia HDI PCB na eletrônica automotiva?
A implementação da tecnologia HDI PCB na eletrônica automotiva vem com seu conjunto de desafios.
Confiabilidade e Durabilidade: Os aparelhos eletrônicos automotivos estão sujeitos a condições ambientais adversas, incluindo variações de temperatura, vibrações e umidade.Assegurar a fiabilidade e a durabilidade dos PCB HDI nestas condições torna-se crucialOs materiais utilizados, incluindo os substratos, laminados e acabamentos de superfície, devem ser cuidadosamente selecionados para suportar estas condições e proporcionar fiabilidade a longo prazo.
Integridade do sinal: a eletrônica automotiva geralmente envolve transmissão de dados de alta velocidade e sinais analógicos sensíveis.Manter a integridade do sinal torna-se um desafio nos PCB HDI devido ao aumento da densidade e miniaturizaçãoQuestões como a intermitência, a correspondência de impedância e a degradação do sinal precisam ser cuidadosamente gerenciadas por meio de técnicas de projeto adequadas, roteamento de impedância controlado e análise de integridade do sinal.
Gerenciamento térmico: os aparelhos eletrônicos automotivos geram calor e uma gestão térmica eficaz é essencial para o seu funcionamento confiável.podem ter densidades de potência aumentadasConsiderações adequadas de concepção térmica, incluindo dissipadores de calor, vias térmicas e mecanismos de arrefecimento eficazes,são necessários para evitar o sobreaquecimento e garantir a longevidade dos componentes.
Complexidade de fabricação: os PCB HDI envolvem processos de fabricação mais complexos em comparação com os PCB tradicionais.A montagem de componentes de pitch fino requer equipamentos e conhecimentos especializadosOs desafios surgem na manutenção de tolerâncias de fabricação apertadas, na garantia de alinhamento preciso de microvias e na obtenção de altos rendimentos durante a produção.
Custo: a implementação da tecnologia HDI PCB na electrónica automotiva pode aumentar o custo global de fabrico.e medidas adicionais de controlo da qualidade podem contribuir para maiores despesas de produçãoO equilíbrio entre o fator custo e o cumprimento dos requisitos de desempenho e fiabilidade torna-se um desafio para os fabricantes de automóveis.
Conformidade regulamentar: Os eletrônicos automotivos estão sujeitos a normas e certificações regulamentares rigorosas para garantir a segurança e a confiabilidade.Implementar a tecnologia HDI PCB ao mesmo tempo em que se cumprem estes requisitos de conformidade pode ser um desafio, uma vez que pode envolver processos adicionais de ensaio, validação e documentação.
Para enfrentar estes desafios, é necessária uma colaboração entre os designers de PCB, fabricantes e fabricantes de OEM automotivos para desenvolver diretrizes de design robustas, selecionar materiais adequados,Otimizar os processos de fabrico, e realizar testes e validações exaustivas.Superar estes desafios é essencial para aproveitar os benefícios da tecnologia HDI PCB na electrónica automóvel e fornecer sistemas electrónicos fiáveis e de alto desempenho nos veículos.